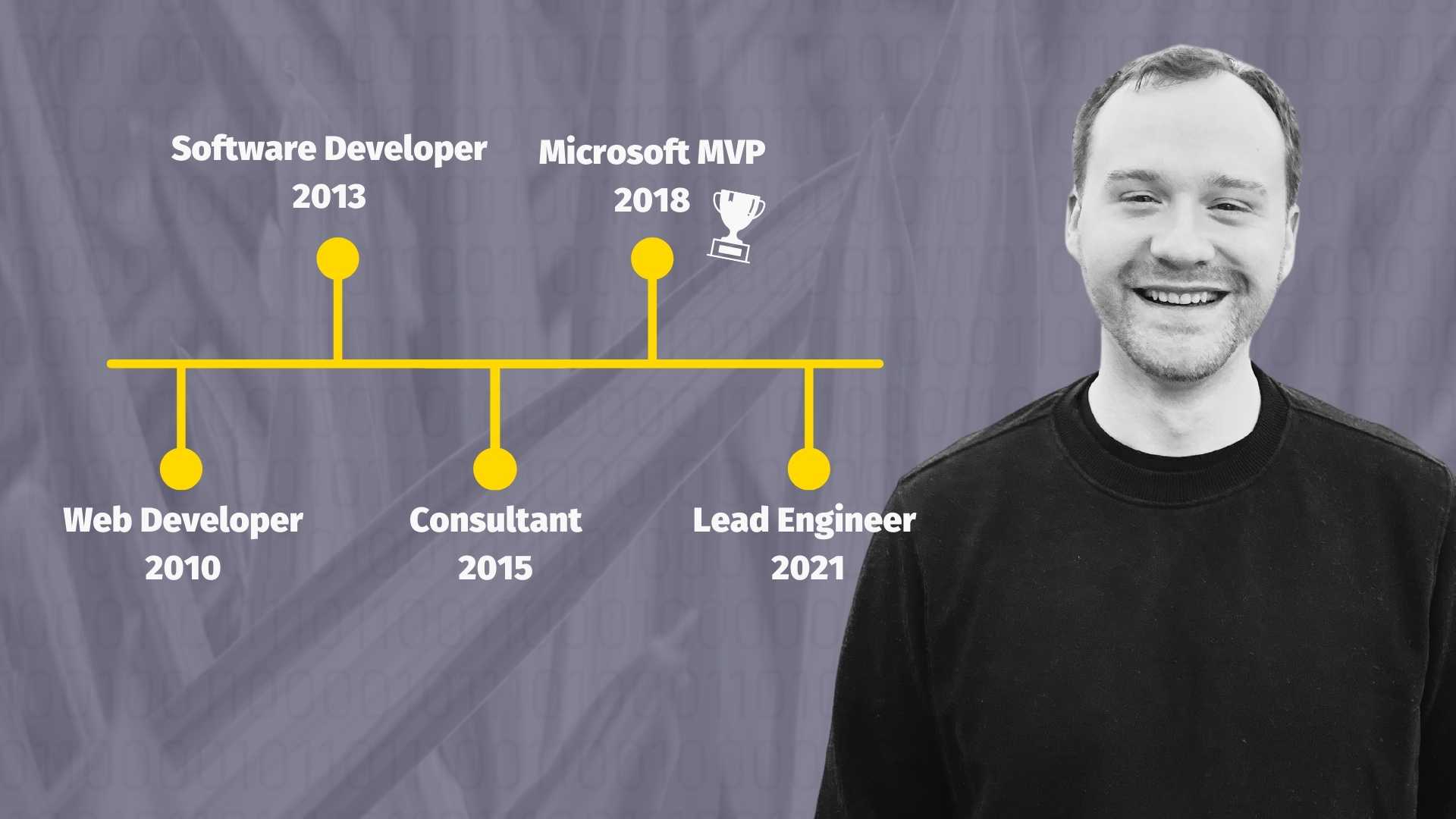
Leverage My Experience
Hi! I’m Jared, and I’ve been doing software engineering for a little while now. I’ve stuffed nearly everything I’ve learned about the software engineering hiring process into a dang-near complete guide that will help you break into software engineering.
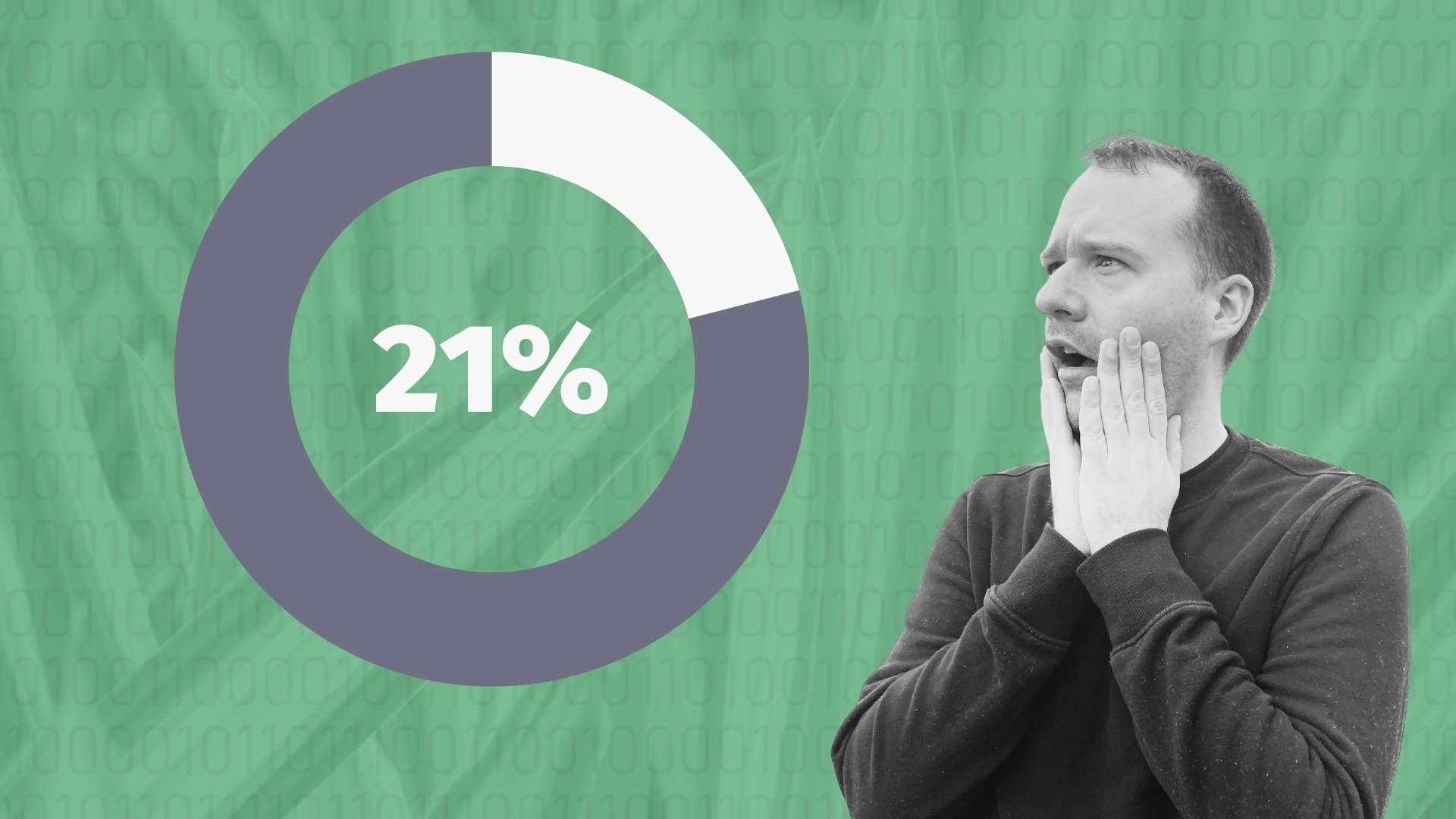
The Shocking Statistic
180 days after graduating, 21% of coding bootcamp grads don’t yet have a job as a software engineer. For college graduates, the average time to find a job after graduation is 3 months. I want to help you find and land a better job, faster.
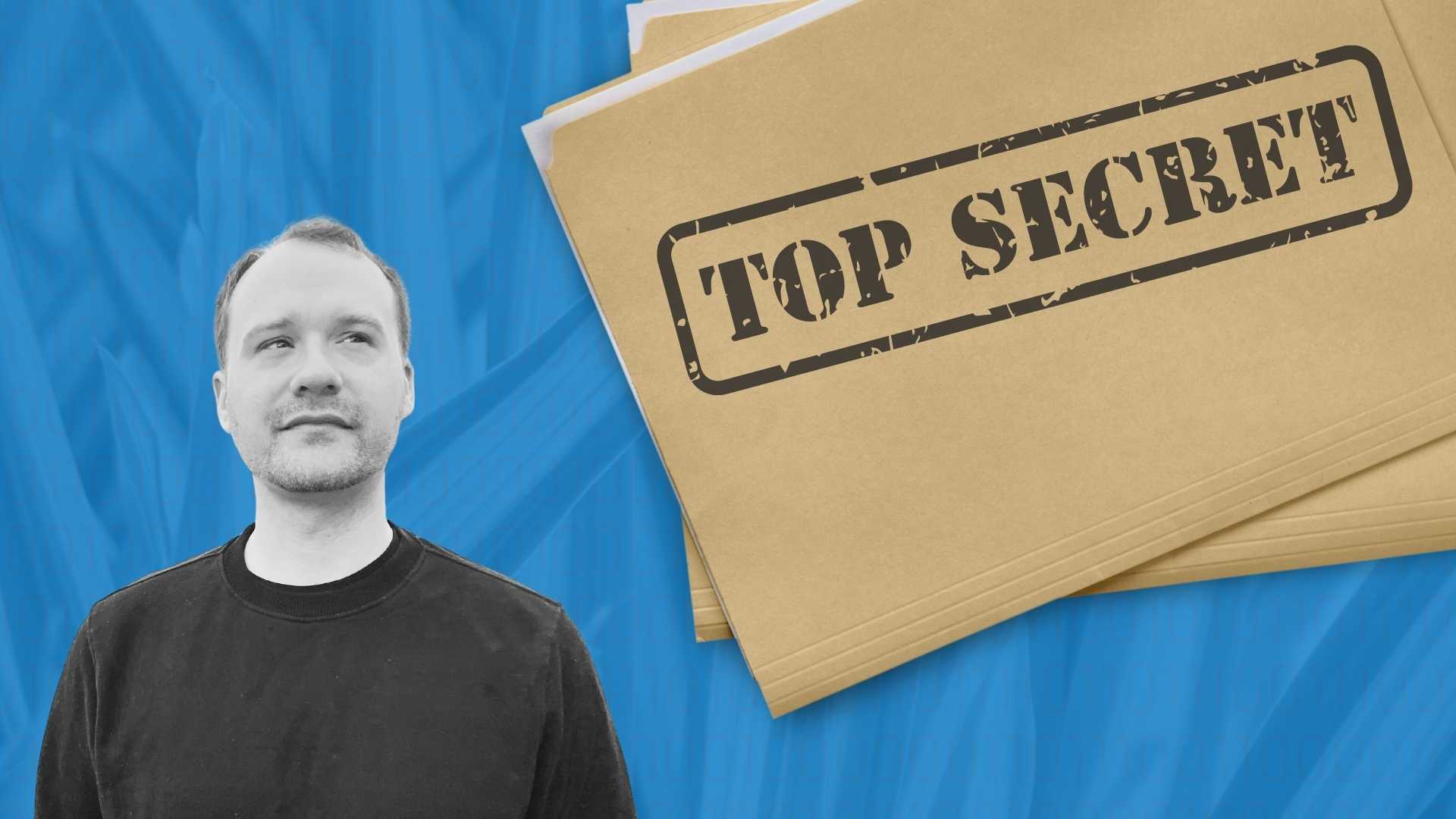
Learn My Secrets
Follow a simple process to finding the employer of your dreams…
Learn the system to get companies excited to meet you before you’ve even applied…
Understand the difference between an offer you should accept and one you should reject…
Handshake Protocol: the step-by-step guide to get hired as a software engineer
$
39
.00
What You’ll Find Inside